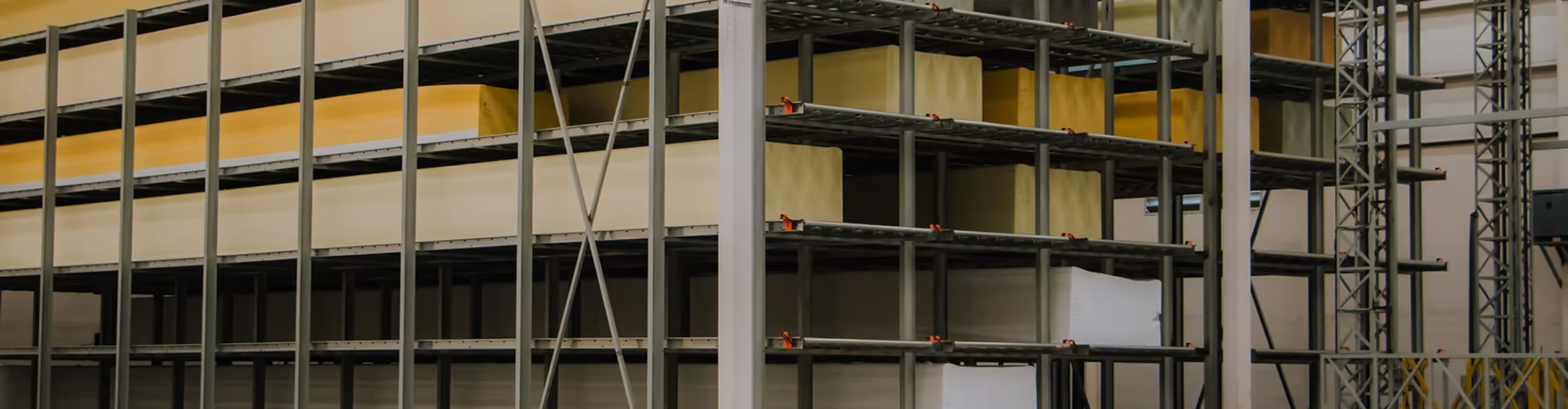
30% more with the same: How Espumas Industriales increased production with Pulsar
To tackle the challenge of consolidating two plants into one operation, Espumas Industriales partnered with Pulsar to gain crucial insights into their processes and significantly boost production.
The Challenge
Espumas Industriales aimed to elevate their family business to the next level of operational excellence. A central part of their strategy was consolidating their two plants—foam manufacturing and mattress production—into one facility. To achieve this, the management team needed a clear and detailed understanding of their production capacity and faced a critical decision: whether to invest in expensive, high-capacity machinery to support their growth.
The primary challenge for Espumas Industriales lied in its productivity metrics. At the time, the team depended on broad indicators like units produced or meters of foam manufactured to track efficiency. However, they lacked a system to analyze machine downtime effectively. For Espumas Industriales, it was crucial to quickly enhance its operational management to meet its business objectives.
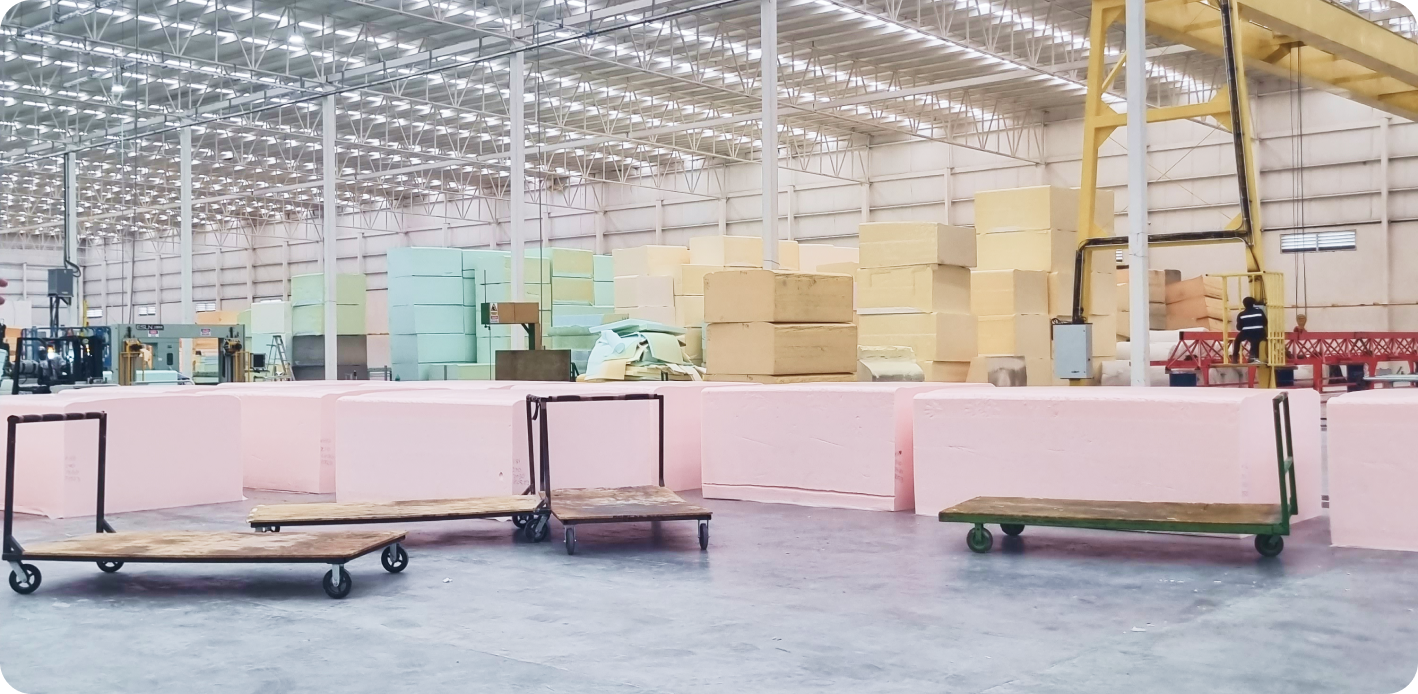
The Solution
Espumas Industriales began its journey with Pulsar in early 2022. After a successful pilot, they selected nine machines—prioritizing those with the highest production volumes—to monitor their real-time performance. Within weeks, they gained critical insights into where to begin transforming their operations: two of their key machines, known as peelers, were operating inefficiently due to frequent downtime.
"We realized that using just one machine could still meet our production goals."
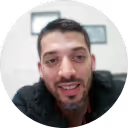
By leveraging Pulsar's real-time indicators, historical reports, and operator-logged downtime causes, the team identified material setup as the primary driver of machine downtime. With this insight, they implemented strategic actions to improve operational efficiency:
- focused on optimizing the operation of a single peeler machine rather than running two simultaneously;
- streamlined material setup by assigning a dedicated staff member; and
- reduced one complete shift by reducing downtime.
Along with operational changes and with management's support, Espumas Industriales implemented continuous improvement programs, training initiatives, and incentive plans for operators to drive Pulsar adoption.
Real-time monitoring of cutting and foam manufacturing machines
Data recording and analysis to support continuous improvement programs
Performance metrics for plant workforce incentive programs
Remote plant monitoring
Results
Fueled by Pulsar's insights, the Espumas Industriales team increased key machine availability by 110%, eliminating bottlenecks, optimizing shifts, and gaining deeper insights into their critical performance indicators.
These improvements helped the company make a key decision and opted not to make additional machine investments, as they optimized their existing infrastructure and assets to achieve a 30% increase in production across key processes.
Additionally, through their training and incentive programs, they achieved over 90% logging of downtime causes by operators, ensuring full transparency and clarity in plant operations.
Thanks to these enhanced production capabilities, the company relocated operations to a more prominent Salinas Victoria, Nuevo León facility as part of their business consolidation strategy. Today, Espumas Industriales is moving into a new phase of growth, fully supported by their team and Pulsar's data-driven platform.
Benefits
Explore our platform
Explore more success stories
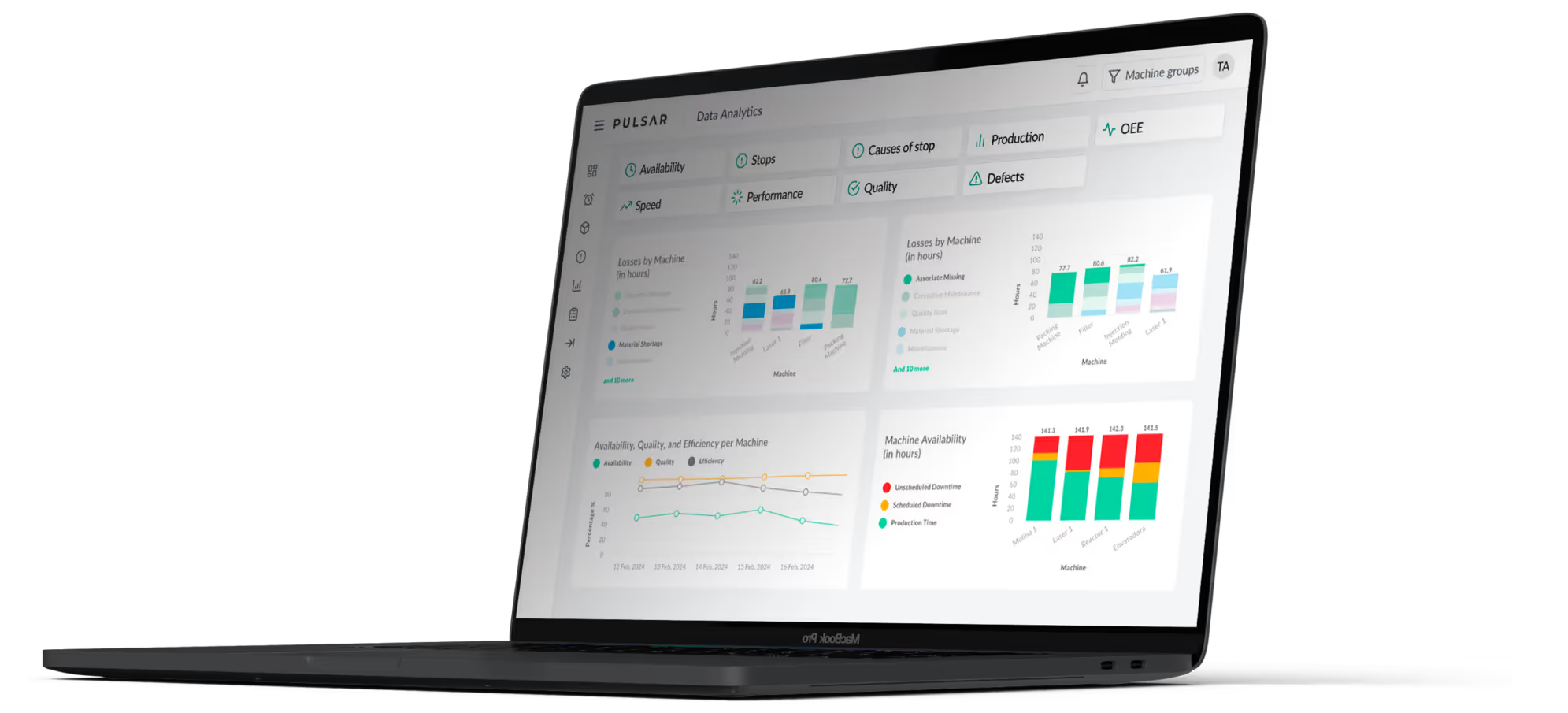
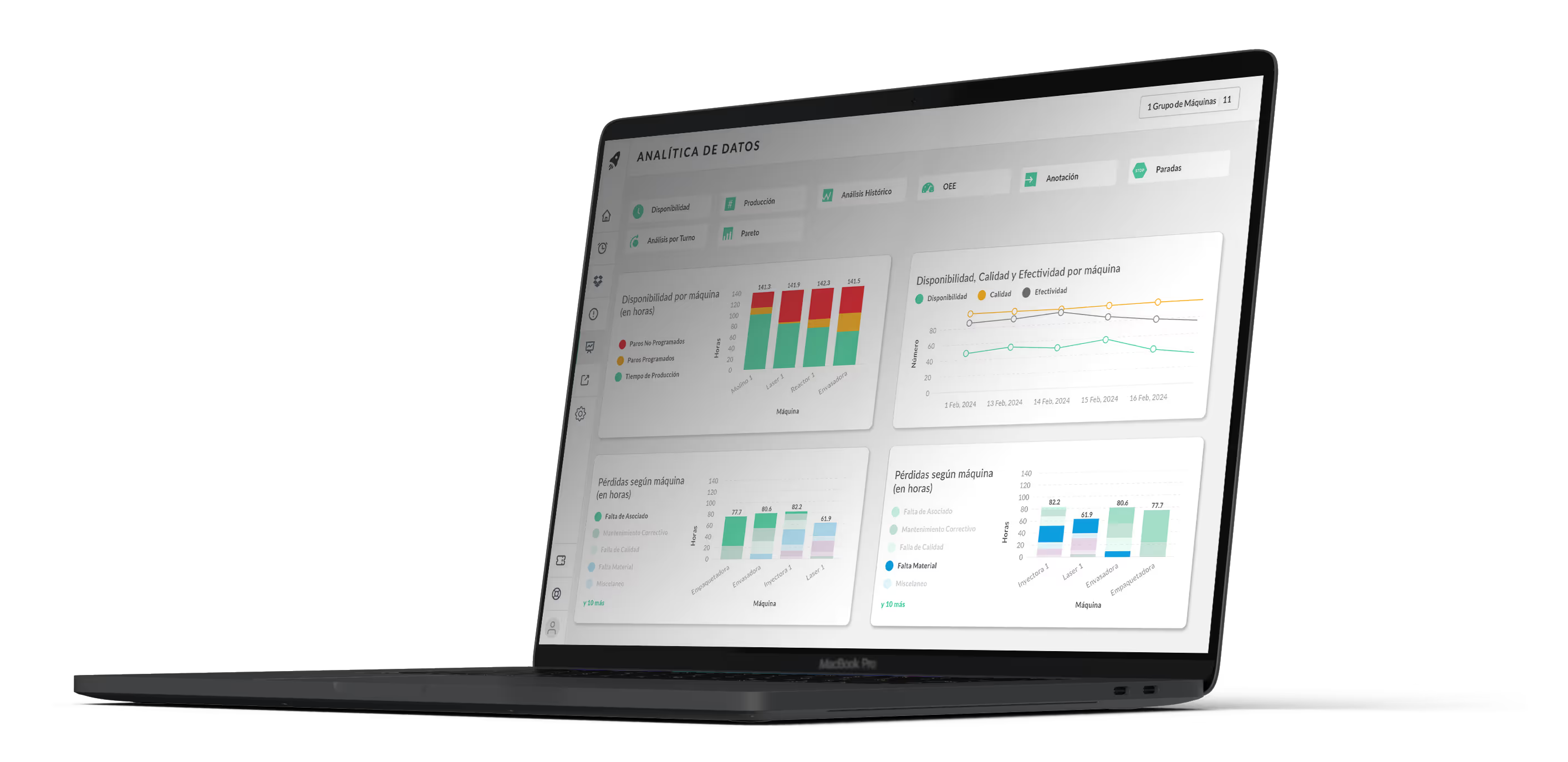
Request a Custom Demo
See how our production control and OEE monitoring platform can optimize your processes.
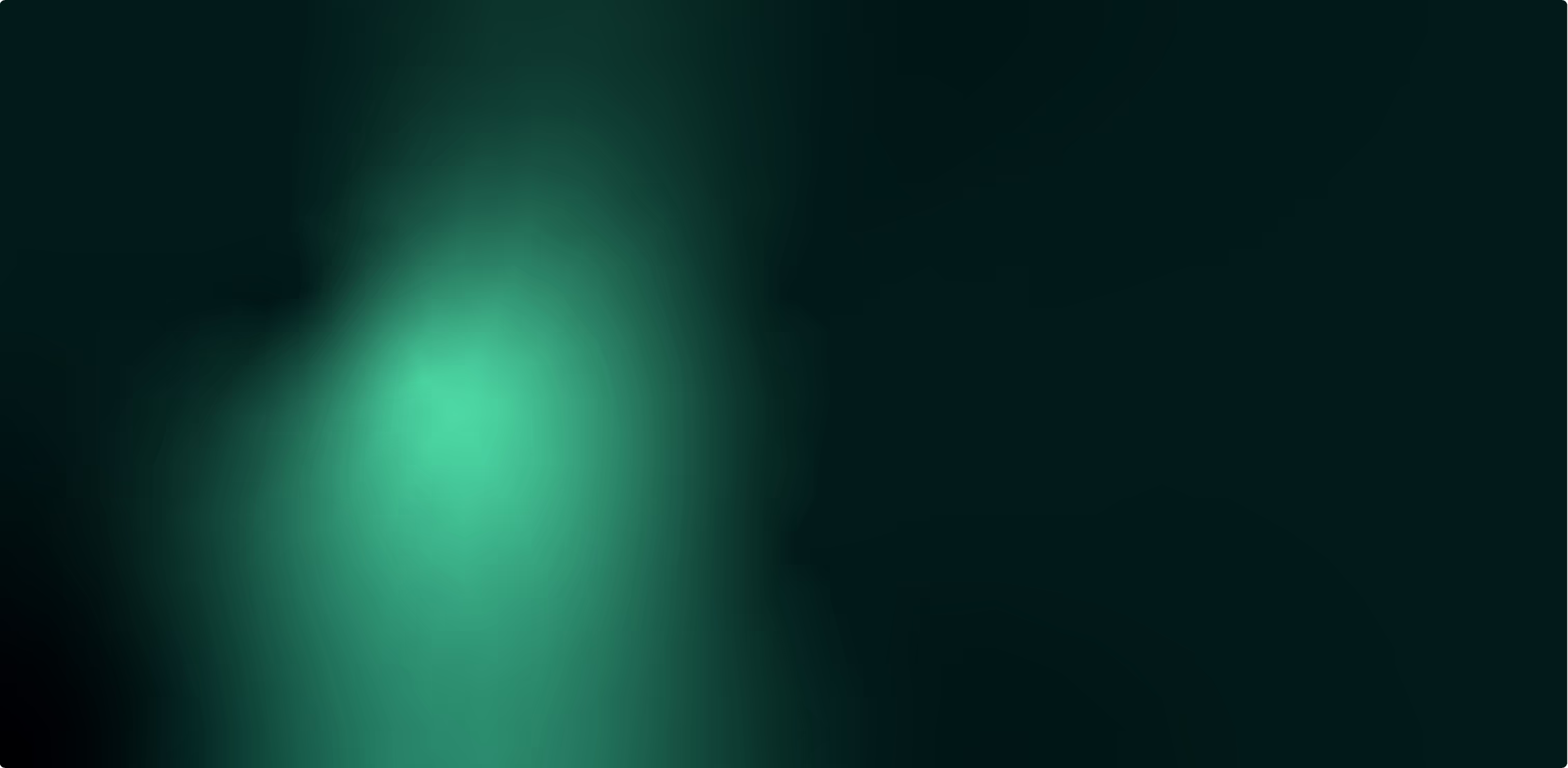