
Agile, expert-led implementation with full support

Expert support for a successful Digital Transformation
Effective change management is crucial when implementing Industry 4.0 projects in industrial plants. Our Customer Success Program ensures a seamless transition, guided by experts at every step, to make adopting our platform effortless.
Customer Success Program
One-Visit Installation
Tailored Implementation Plan
Training and Onboarding
Continuous Technical Support
Custom Software Setup
Customer Success Partner

"The attention, dedication, follow-up, support, and guidance provided by Pulsar have been instrumental in delivering a great experience."

Rolando Juárez
Opex Director at Evco
Three foundations for seamless implementation
Single-visit installation without stopping operations
We install sensors, optimize AI/ML algorithms, and tailor the platform to your operations—without halting production—so you can start benefiting immediately.


Training and follow-up program
We provide in-person or online training, ensuring your team quickly masters the platform and stays updated with new features.
Ongoing hardware and software support
Our subscription model ensures dedicated, timely support to keep your platform running at peak performance.

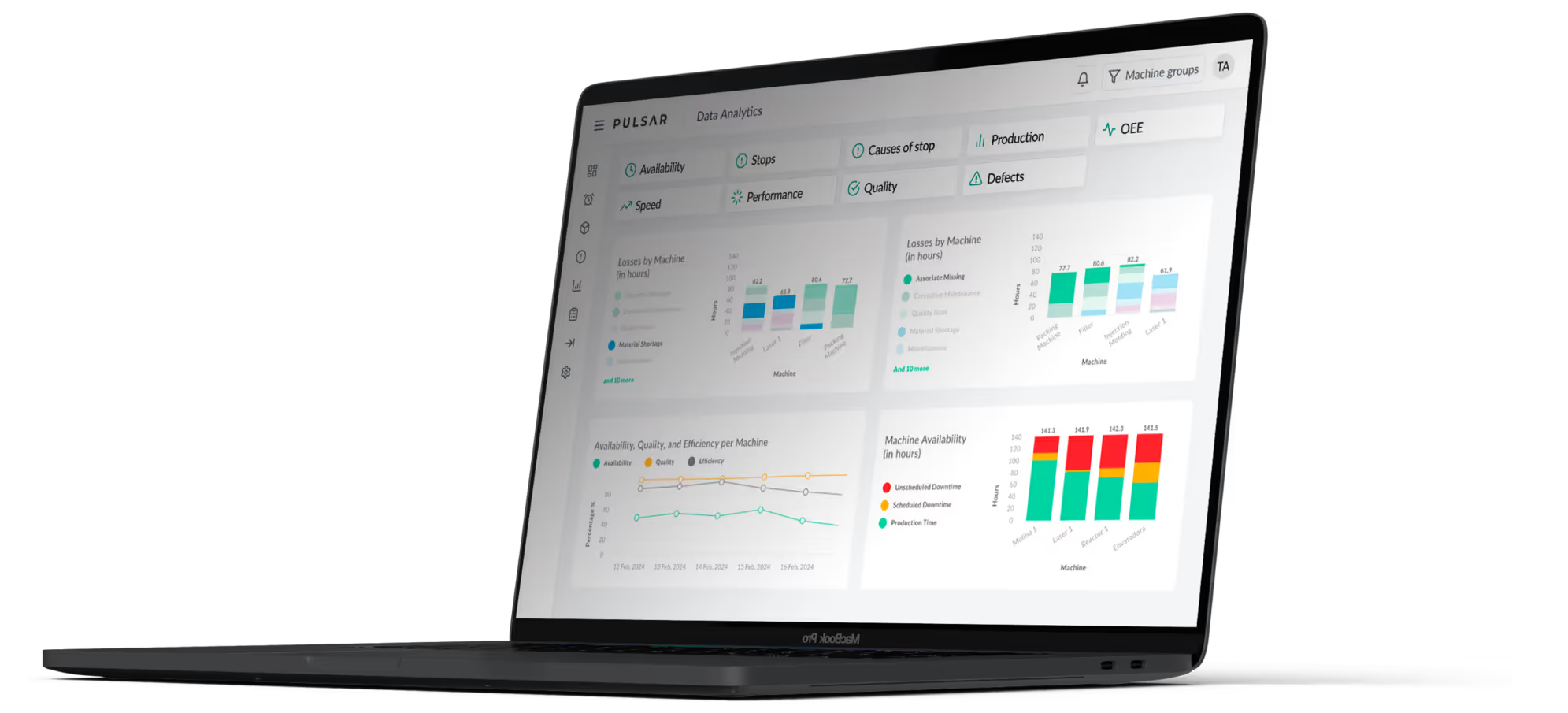
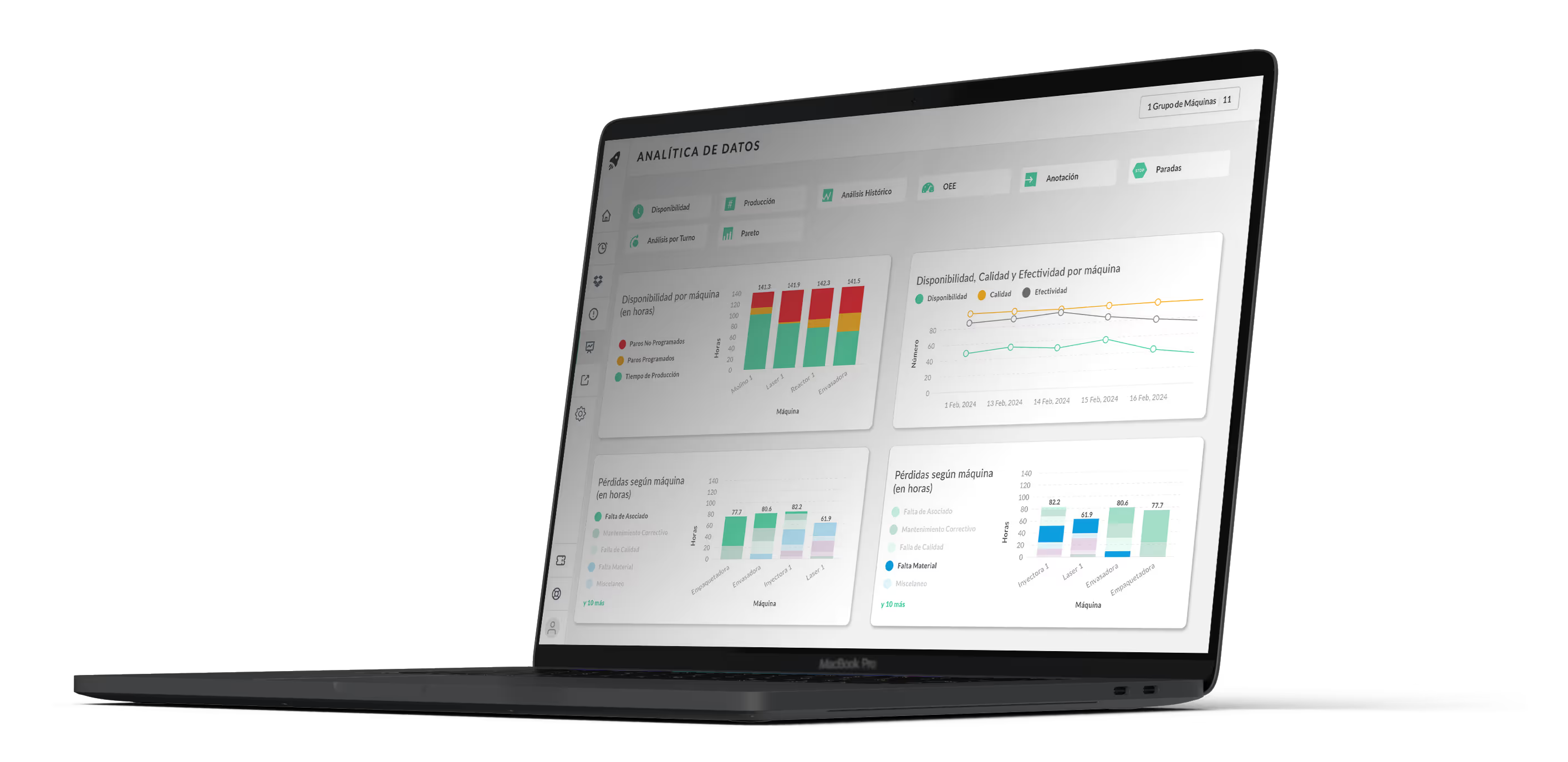
Request a Custom Demo
See how Pulsar’s OEE machine monitoring can help your operations today.
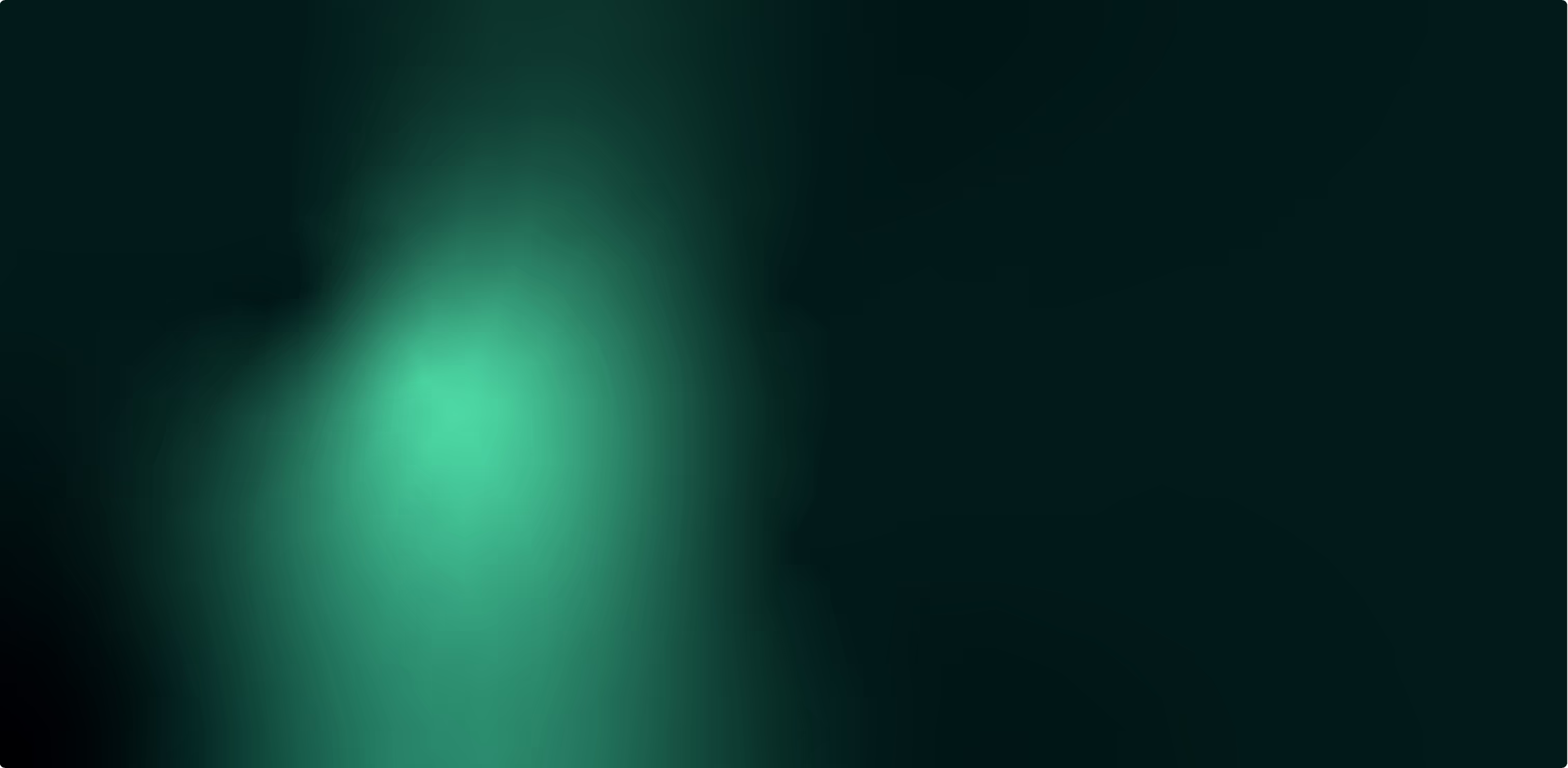